Project Overview
The main Roll On – Roll Off (RoRo) terminal at Fisherman’s Landing supplying Curtis Island suffered from extreme erosion caused by vessel thruster wash. The erosion caused regular closures of the ramp, delaying deliveries to the island and impacting the construction program.
The concrete panel ramp was constructed on a rubble mound core, protected with a rock filter layer and D500 armour rock. The vessel thruster wash velocity was approaching 10 knots at the thruster or 4.5m/s at the seabed during departure. This in turn was dislodging the armour rock and scouring the toe of the ramp, causing its collapse.
The client’s base case design for the repair was to remove the armour rock, rebuild the ramp and armour the ramp with a geotextile back mattress. This plan would require a one month shut down of the berth and cause major disruption to the construction program on the island.
MMA's Solution
We redesigned the armour system to maintain the existing core and armour, overlaid with a high-performance scour solution. This solution enabled the installation to take just one week - greatly reducing disruptions to island construction.
We designed and supplied the scour protection system for the FLNE RoRo Ramp, including:
- Engineering design of concrete mattresses and associated anchors
- Fabrication of mattresses
- Provision of installation supervision and lifting frames
Outcome
With our solution, the ramp was repaired within 10 days working around the supply vessel schedule. Additionally, the ramp did not need to be closed for maintenance for the remaining five years of the construction project.
Technical Details
|
Dimensions (m) |
Dry Weight (Te) |
Quantity |
1 |
0.3 × 6.0 × 2.0 |
5.5 |
9 |
2 |
0.3 × 5.5 × 2.0 |
5.1 |
1 |
3 |
0.5 × 6.0 × 2.0 |
8.5 |
88 + 2 spare |
- 16mm 316 SS IWRC wire reinforcing and lift points
- 12mm 316 SS Interconnecting Bow shackles
Design Specifications
- Seabed design velocity 4.5m/s
- Water Depth 0m - 8m
- Edge Stability Factor of Safety = 1.5
- Anchors driven to 1.5m depth (every 2m on the ramp sides)
- Design Methodology = Pilarczyk 2015
- UV stability for shallow water applications
Key Equipment / Installation Method
- We provided two onshore frames to facilitate simultaneous loading and unloading of the trucks at the hardstand and quayside respectively
- Mattresses were installed using a diver operated lifting frame
- The mattresses were case using stainless steel wire and interconnected using stainless shackles
MMA Innovation / Value Added
- Our solution enabled the ramp to be re-armoured to survive a higher design velocity
- We produced custom mattresses to fit tightly around the fender piles
- We deployed an effective anchoring system on the leading edge of the mattress array
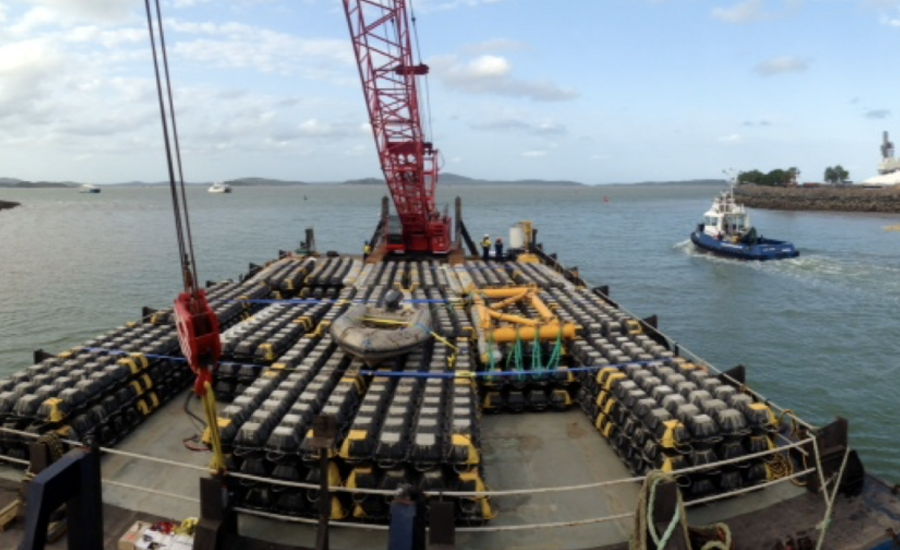