Project Overview
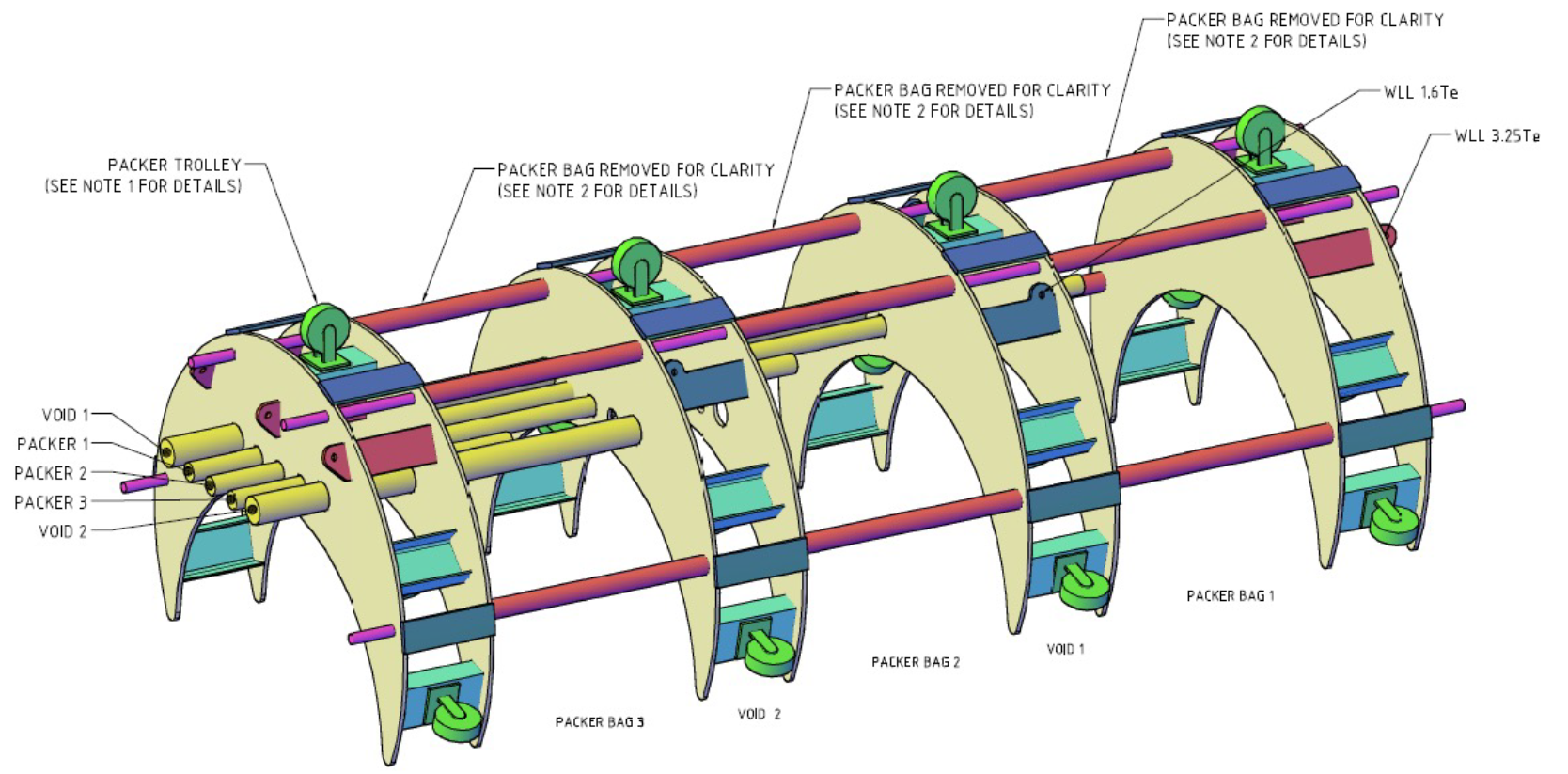
The Wheatstone Project is one of Australia’s largest resource developments and Australia’s first liquefied natural gas (LNG) hub. Wheatstone’s onshore facilities are located at Ashburton North, 12km west of Onslow on the Pilbara Coast of Western Australia.
A 225km trunkline transports gas from the Wheatstone platform to the onshore facilities at Ashburton North. The 44” trunkline crosses a shoreline with a very high environmental value, comprising complex geology and a tidal lagoon.
The micro-tunnel option for the shoreline crossing was specified because it was less sensitive to difficult geotechnical conditions and avoids environmental impacts associated with other shore crossing methods, minimising the onshore and marine footprints.
MMA was contracted by Dredging International to conduct the grouting of the trunkline into the micro-tunnel in 2014. Achieving a seal in an annulus between two pipelines, 70m into the tunnel and underwater in zero visibility conditions is complicated.
MMA's Solution
The scope of work involved designing and installing a grout seal in the annulus of the mirco-tunnel just below LAT to seal against tidal movement and anchor the pipeline against thermal expansion so it did not transfer loads into the LNG plant. The seal was set in two stages with an initial packer inflated to seal the annulus before the tunnel was mass filled with a high-performance grout.
Outcome
The annulus packer was set 70m from the entrance to the micro-tunnel. We deployed the packers on a packer trolley complete with pipework preinstalled. The packers were then remotely inflated with grout pumped from the shore to provide a positive seal and prevent seawater ingress. Once the plug was set, the tunnel was dewatered to minimise the environmental impact of the grouting. After the top 70m of the tunnel was dewatered, 120m3 of ultrahigh- performance grout was placed behind the plug with a near-horizontal pour, thus securing the export trunkline and protecting against corrosion in the intertidal zone.
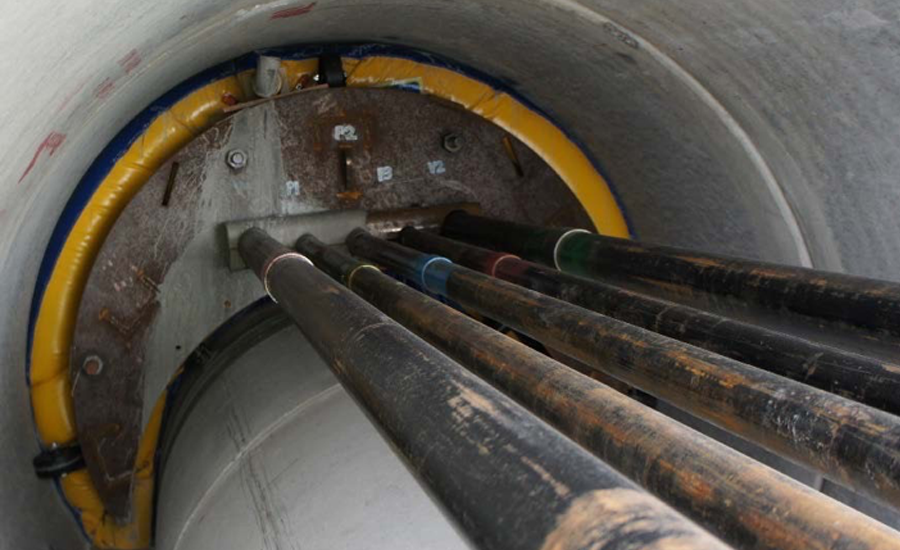
Key Equipment / Installation Method
- Original concept
- Full scale System Integration Testing (SIT)
- Engineering of packer train and bespoke fabric formworks
- Ultra-high-performance grout
Technical Details
- Micro-tunnel Nom Diameter: 2.5m
- Trunkline Outer Diameter: 1,245mm
- Packer Grout: Masterflow 700
- Annulus Grout: Masterflow 871
MMA Innovation / Value Added
We were able to carry out a large, mass pour of high-performance grout into a high-temperature environment, 70m into a tunnel. The lack of accessibility posed some interesting workability challenges. The MMA team overcame these with the following innovations:
- A full-scale mock-up of the tunnel and packer deployment system to prove the placement methodology
- System of packer and pipework trolleys which enabled accurate placement of the packers and grout within the tunnel
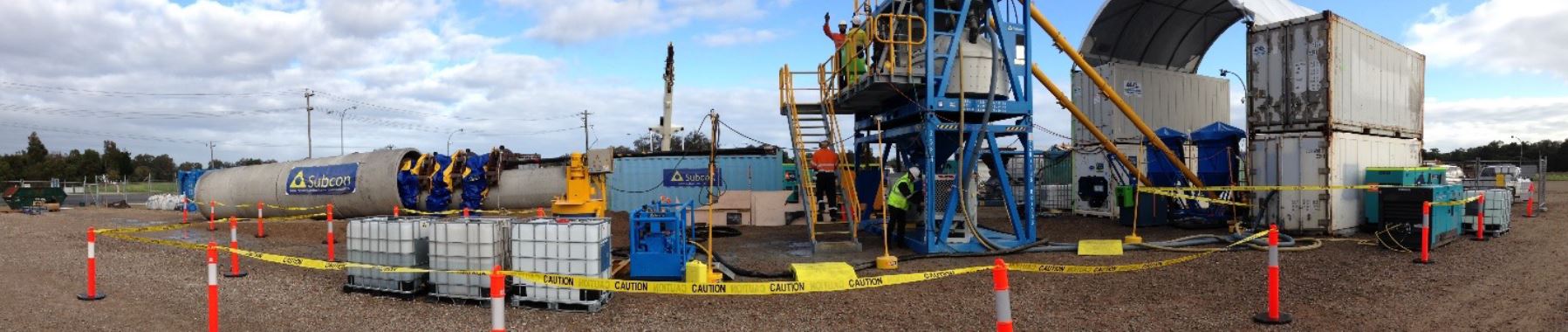